How do pump stations work?
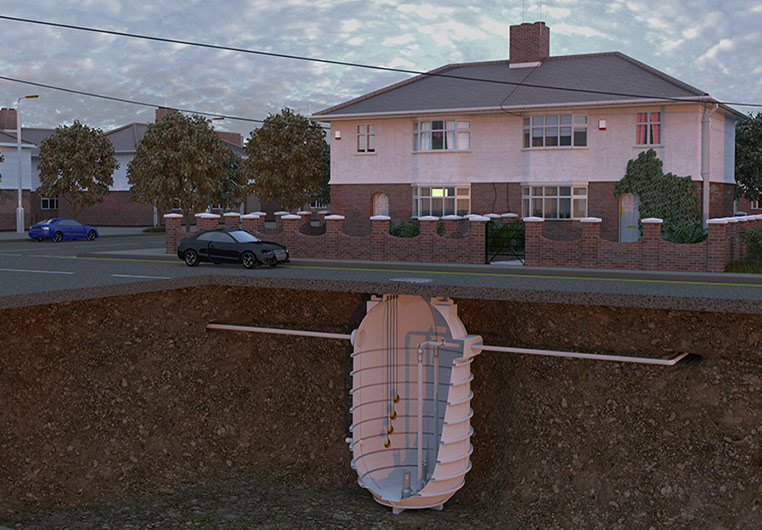
In many ways, the pump station is an underrated and often overlooked utility in day-to-day life and the everyday maintenance of business productivity. Pump systems are crucial to so many residences and commercial settings.
Pump stations control water levels and enable the transportation of water away or toward a source. Because they’re underground or out of the way, people often forget they’re there, tirelessly working away.
Plus, even looking at a pump station doesn’t give you a real understanding of how it does what it does—most likely because everything happens inside a casing or a ‘pit’ and most people are not pump pros.
In this guide, we’ll explain how pump stations work, what they’re made of and who you can contact for your pumping solutions.
What is a pumping station?
A pump station, sometimes known as a packaged pump station, is a storage/collection chamber that contains a pump set. The internal pump set is designed to transfer foul, stormwater or surface water to a nearby drain, manhole, or sewer.
Pumping stations are installed into a larger water/sewage network or series of pipes. Ordinarily, the network of pipes relies on gravity for the waste to flow into the main sewer. However, in low-lying areas or areas with higher fluid volumes, with the main sewer sitting on higher ground than the domestic sewage pipes, the fluid needs to be transported differently. This is where pumping stations are utilised.
What does a pumping station do?
Water pumping stations transport fluid and/or sewage from one site to another. Pump stations are integral parts of residential and commercial premises, with specific pump systems installed to deal with demand.
A pump station can impact the rate at which water flows, break down contaminants in wastewater and redistribute fluids where they need to go. Pumping systems can also be used inside factories to control the excess produced often known as effluent.
What pump stations can do is only limited by their design. Bespoke pump stations can be adapted and built to deal with niche requirements and a correctly specified pump can enable lots of needs are solved.
From removing excess water and sewerage from a new railway station to discharging washdown from a chocolate factory production line, pump stations are critical in many applications to keep operations running.
How are pump stations specified?
Pump stations are specified by calculating how much product has got to be moved, at what flow-rate and the distance and height it has to travel to point of discharge. The size of the storage tank can depend on what storage is required e.g., a housing development may need to have 24-hours storage capacity in the tank whereas a production line may only require a few hours storage as they have critical spares on-site for immediate repair.
Building regulations state that a pump station for housing requires 24-hour storage below the lowest incoming invert (this is the lowest pipe feeding into the tank). This prevents backing up the system in the event of a pump blockage/failure and gives engineers a day to get the issue resolved before it causes any inconvenience to the residents.
Pump stations can be specified as above ground or below ground, this can depend on a variety of factors such as water table levels in the ground etc.
How do pump stations work?
Above we’ve covered what pump stations do, but how do they do it? Pump systems are the middle-ground between the source and the final stage. They are made up of lots of different sections (that we’ll cover below), neatly combined to create one unit that transfers produce that enters into the tank to the point of discharge at the end of the rising main.
They are programmed to discharge the produce from the tank when it reaches a certain level, this is so that they are not constantly running and also can discharge at the specified flow rate for a controlled amount of time.
What are the different parts of a pump station?
To give you an idea of how a pump station is put together, we’ll use the submersible pump as an example.
The product will flow into the tank via one of the inlet pipes and the pump is submerged in the liquid. The tank will continue to fill until a float switch triggers the pump into action causing it to discharge. The tank will then continue to empty until another float switch stops the pump from running when the level is at the top of the pump. The pumps must stay submerged in liquid as this provides cooling for the motor.
This pump body is connected to a pump stool, also known as a pedestal, by a piece of equipment known as the claw. This claw is not only a connector but also slots into the guide rails so that the pump can be removed easily for maintenance.
The stool is connected to the non-return valve by a pipe, usually curving up to raise the height. The non-return valve stops water from flowing back into the main tank. The last piece of the pump puzzle before the fluid reaches the discharge pipe is the gate valve or isolator valve. There is a non-return valve installed on the discharge pipework which stops the fluid flowing back into the tank. The fluid will pass through this and under a gate-valve and into the rising main, the gate valve is installed so that the tank can be isolated should any maintenance work need to take place.
Pumping station pits or tanks are usually 1m/1.8m/2.5m/3.5m in diameter and can go up to 5m in depth in standard sizes. Anything over 5 metres is usually considered a specialist product.
These pits, or tanks, are constructed from strong materials such as plastic, GRP or concrete. They are designed to withstand their environments and keep the pump systems inside secure.
When it comes to keeping control over the water levels, floats are hung from the top of the pit into the water. The floats are connected to a control panel and as the levels rise and fall they are activated and deactivated.
A standard packaged pump station control panel is pretty simple and can have over six lamps on the front to indicate the status of the pump system on the panel. Should the fluid levels in the pump reach a beyond safe level, the control panel will indicate with lights and sound to the controller.
Twin pump stations control four floats at different levels of suspension. The lowest hanging is stop, which will prevent the pump station from working when the water levels are too low. The next is start. This is followed by assist and high level. All of these levels are transferred back to the control panel.
What different types of pump stations are there?
As mentioned, there are lots of different pumps such as grinder pumps which break down the larger products in the fluid before passing through the volute and up the rising main. Submersible pumps are most commonly used in pump stations but come in variations such as the grinder pump that are more accustomed to dealing with contaminants in the water such as sand or small refuse.
Interceptors are typically plastic or ceramic tanks installed before the pump system network or natural water flow and can catch and contain contaminants, allowing the remaining flow of water to be discharged safely. An interceptor is essentially a large trap that is inserted to filter the pollutants from runoff before they enter a watercourse or stream.
We don’t only deal in pump stations and the associated pumps, we deal with a large range of pumps for varying industries. We have provided a couple of examples below:
Heating pumps provide heat energy that is transferred from a source of heat or warmth to a destination called a heat sink, effectively ‘pumping’ warmth from one place to another.
Process pumps are typically designed for transporting produce on a production line and are most commonly found in the food production industry.
Want to find out more about where pumping systems can be used? Check out our extensive range of case studies.
Need a pumping specialist?
At Dura Pump, we know exactly how pumps work and we use that knowledge to make sure you get the correct flow every time. We’re experienced with all types of pump dilemmas but we’re masters at providing the solutions.
From specification to installation, we’re there every step of the way to maximise efficiency and reduce problems.
Want to find out more about how pumps work or are your pump systems giving you problems? Talk to the pump experts today on 01604 648 800 or email mail@durapump.co.uk